When looking for effective ways to insulate a home without breaking the bank, many people have heard about the flash and batt method. This hybrid approach combines the performance of spray foam with the low-cost advantage of fiberglass, making it an appealing choice. In construction, methods evolve based on practices that make sense, but for contractors, adopting an unfamiliar product can be a challenge. The flash and batt technique is a new approach being implemented in the industry, using closed-cell spray foam for an initial layer, followed by fiberglass to create a cost-effective barrier. While some reports highlight its benefits, others remain uncertain, questioning if it’s the right fit for every situation.
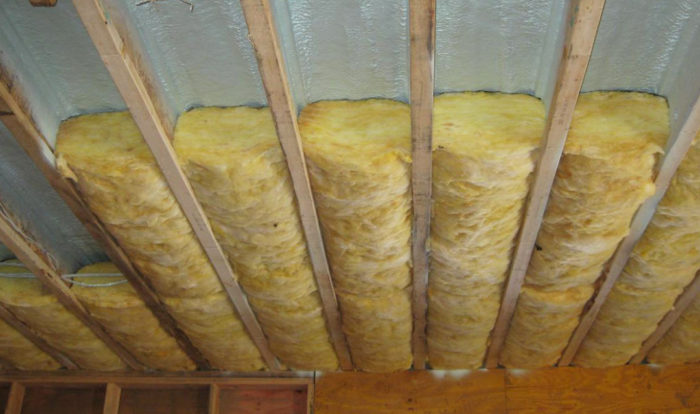
Since the 1970s, fiberglass has been the dominant insulation material due to its affordability, ease of installation, and availability. While simple to install, it often leaves gaps, lacks airtightness, and performs poorly in cold climates. Additionally, it does not act as an air or vapor barrier, limiting its protection. Despite these shortcomings, fiberglass remains widely used, but to enhance performance, it is often paired with spray foam in the flash-and-batt method. This approach improves thermal efficiency without requiring major changes to the construction process, making it a practical choice for contractors working on standard wall frames in modern buildings.
What Is Flash And Batt Insulation?
Flash and batt insulation is a broad term in the construction industry that refers to a method combining spray foam and fiberglass batts to improve insulation. This technique is often used by contractors to enhance energy efficiency while keeping costs lower than full closed-cell spray foam applications. The combination involves applying 1 to 2 inches of spray foam to the interior of a building’s sheathing, creating an air seal, and then placing fiberglass batts over it. This effort helps insulate standard stud walls, typically framed with 2×6 vertical studs, spaced 16 inches on center, and finished with drywall, OSB, plywood, and an exterior siding layer protected by a water-resistant barrier (WRB) like Tyvek.
This system, sometimes called flash-and-fill, differs from other insulation methods like SIPs (structural insulated panels), as it does not fundamentally change the wall assembly but instead augments it. While it provides a higher R-value than fiberglass alone, it does not eliminate all cons, such as potential air gaps in bays or differences in insulation across the wall. However, when used correctly, it can be an effective solution in modern insulated panel concepts that balance pros and cons for energy efficiency and affordability.
Pros of Flash and Batt Insulation Over Spray Foam
Flash and batt insulation is a smart choice for homeowners looking to cut costs on their exterior walls without compromising performance. Unlike spray foam, which can be expensive, this method combines the benefits of both materials to create an efficient and budget-friendly solution. This section covers the two main benefits of flash and batt: improved insulation at a lower cost and better flexibility for different construction needs compared to full spray foam applications.
Flash and Batt: A More Cost-Effective Alternative to Spray Foam
For budget-conscious homeowners, flash and batt is a more affordable way to properly insulate an exterior wall compared to the cost of spray foam insulation. Traditional closed-cell and open-cell spray foam can be expensive, with prices averaging $4.35 per square foot for closed-cell and $2.00 per square foot for open-cell. In contrast, flash and batt combines one inch of closed-cell spray foam, followed by fiberglass batts, creating a hybrid approach that reduces costs while maintaining insulation efficiency.
With a total cost ranging between $2.15 and $4.75 per square foot, flash and batt is a budget-friendly option that provides a decent level of insulation without the high price tag of full spray foam. The R-value of fiberglass batts is lower, but supplementing it with spray foam enhances performance. This application is an accessible and good alternative for those looking to reduce expenses without sacrificing efficiency, making it a practical choice for many homeowners.
Flash and Batt: A Better Choice for Sound Control Than Spray Foam
When it comes to sound attenuation, flash and batt offers better noise control than closed-cell spray foam, making it a great option for homes in noisy areas. While spray foam is commonly used for insulation, its cell structure is rigid and does not allow sound to be absorbed or quieted effectively. In contrast, fiberglass has sound-dampening qualities, which help trap noise pollution and create a quieter environment.
By combining materials, flash and batt enhances acoustic properties in exterior walls, offering an improved reduction in noise compared to using spray foam alone. This application is particularly beneficial for thin-walled homes where better sound control is needed. The fiberglass layer acts as a buffer, reducing outside noise and creating a more peaceful neighborhood experience.
Pros of Flash and Batt Insulation Over Fiberglass Batts
When choosing insulation, it’s important to consider how different materials affect performance. Flash and batt offers a more effective solution than fiberglass batts by combining closed-cell spray foam with traditional insulation. While fiberglass batts alone provide some insulation, adding an inch of spray foam enhances the wall’s efficiency, reducing air leaks and improving durability. When you compare the two main benefits, flash and batt insulation stands out as a better option because it balances cost and performance without the drawbacks of fiberglass alone.
Flash and Batt: A Better Air Barrier Than Fiberglass Alone
One major advantage of flash and batt insulation is its ability to create an airtight layer, something fiberglass batts alone cannot achieve. While fiberglass is a popular and affordable insulation material, it lacks air-sealing ability and does not prevent air leakage, which leads to decreased efficiency. In contrast, adding spray foam fills gaps, boosts performance, and reduces heat loss by sealing off exterior walls. This method also helps support HVAC equipment by maintaining better air quality inside the home.
By combining 2 inches of closed-cell spray foam with fiberglass batts, the flash and batt system significantly improves thermal efficiency while keeping costs lower than full spray foam applications. The R-value of insulation materials is traditionally used to determine how well they prevent conductive heat flow, but air-seals are just as important in stopping radiation and convection. Unlike normal cellulose, which is air-permeable, flash and batt insulation acts as an effective air barrier, preventing movement through the sheathing and reducing the risk of energy waste.
Flash and Batt: A Higher R-Value Than Fiberglass Alone
Flash and batt insulation provides a higher R-value compared to using fiberglass alone, making it a better choice for energy efficiency. While fiberglass batts are established in the market, they often perform poorly due to gaps, sags over time, and compromised installation, which allows air-flow, heat transfer, and conditioned air to escape. This lowers insulation performance, making it less effective in extreme temperatures.
By adding a layer of closed-cell spray foam, flash and batt significantly boosts insulating capabilities, improving the wall cavity’s thermal resistance. A single inch of spray foam can add R-7, while 2 inches can replace traditional R-3.5 per inch fiberglass for greater efficiency. This radical improvement enhances standard wall systems, achieving R-13, R-19, or even R-38 insulation ratings. The aged R-6 resistance of spray foam ensures better long-term performance, helping maintain indoor temperatures more effectively.
Cons Of Flash And Batt Insulation
While flash and batt has its positives, this method is not ideal for all homeowners, especially those leaning toward fiberglass or considering spray foam. Though it aims to boost performance and save a little money, it may still create issues that make it a controversial choice. Some believe it can offer sound control, but the technique does not always work as expected. For customers, there are often better solutions with fewer complications, making it essential to examine the issues in more detail before choosing this method.
Risk of Condensation Issues with Flash And Batt
One of the biggest concerns with flash and batt insulation is its potential to create condensation problems. This method often uses closed-cell spray foam as a portion of the installation, but it does not install enough to act as a proper vapor barrier. To be effective, two inches of spray foam are needed to block moisture, but since only one inch is typically applied, water in its gaseous state can still pass through walls. When warm air meets cold surfaces inside the wall cavity, the humidity reaches its dew point, and the excess air content condenses into liquid, leading to mold, mildew growth, and wood rot.
Since fiberglass cannot seal these gaps or retain moisture, the traditional air-barrier remains intact but incomplete, allowing moisture to travel and settle within the wall system. If left unchecked, this could lead to major insulation failures over time. The risk increases in colder temperatures, where condensation forms faster and spreads quickly, making it essential to address this issue before choosing flash and batt.
Thermal Bridging: A Weakness of Flash and Batt
One major issue with flash and batt is that it doesn’t address thermal bridging, which occurs when heat flows through uninsulated wood studs, reducing overall efficiency. While spray foam provides R-value, the fiberglass layer does little to stop heat flowing through the framing, which compromises the wall assembly. This means the whole-wall R-value is considerably lower than the advertised insulation rating, making it less effective than some standard insulation methods that use continuous framing solutions.
Gapping Issues in Flash and Batt Insulation
One of the most common problems with flash and batt insulation is gapping, which occurs when fiberglass batts do not fit properly in the cavity. Since fiberglass is manufactured in pre-cut sizes, it sometimes ends up bigger or smaller than the space, leaving gaps behind that reduce insulation effectiveness. Unlike spray foam, which adheres to the surface it is sprayed against, fiberglass batts do not adhere and are simply placed or stuffed into cavities. Over time, these batts may settle or sag, leaving wall areas no longer covered enough to insulate properly, leading to cold spots and compromising the entire system’s performance.
These gaps are particularly problematic in areas with condensation issues, as the open spaces become an ideal place for mold to grow. If moisture settles between the layers of spray foam and fiberglass, it could lead to insulation failure over time. Since flash and batt combines two materials with different properties, gapping problems must be carefully addressed to ensure the R-value is not compromised, and the insulation performs as expected.
Higher Cost and Labor Demands of Flash and Batt
One negative of flash-and-batt installations is the added cost, as it combines the same costs of a standard fiberglass-batt job with the expensive application of spray foam. Unlike SIPs, which offer simplicity and allow faster construction, this method actually takes longer and requires more labor due to the time allowance needed for spraying and curing. Even with advanced framing, there are no material savings, making it a costly choice compared to other insulation options.
Flash and Batt Is Not Always Needed for Code Compliance
An insulation contractor may suggest flash and batt to meet prescriptive code, but in reality, the same performance can be achieved using just foam. New construction walls typically need at least R-21, and some builders apply 2 inches of closed-cell spray foam, which provides R-14, then add fiberglass to make up the difference. However, this is often a misguided idea to solve a problem that doesn’t exist, as a well-applied spray foam system alone can meet the required insulation standards.
Environmental Concerns with Flash and Batt
While flash and batt can help conserve energy, it also runs into the energy auditor issue of embodied energy vs. greenness vs. energy saved. Although the whole assembly may perform better than a standard wall, the spray foam component has a higher embodied energy, and its propellants are often non-green and petroleum-based. While there are some products with different ingredients that address these issues, they are considerably less common, making flash and batt insulation a less eco-friendly choice.
Is Flash and Batt Insulation the Right Choice for Your Home?
Deciding whether flash and batt insulation is appropriate for your home requires weighing the pros and cons carefully. While this method offers cost savings and improved sound control, it also has potential condensation issues and installation difficulties, which can be significant concerns in certain climates. In regions like Michigan, where vapor barriers are necessary, alternatives may be more reliable. Before making a decision, it’s essential to consider how well flash and batt fits your specific needs and climate conditions.
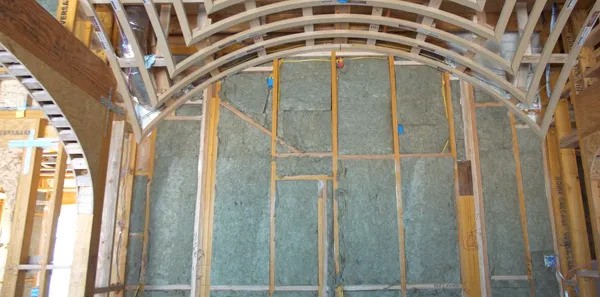
Exploring Hybrid Insulation for Better Performance
For those looking for hybrid insulation methods, consider exploring options that incorporate vapor barriers for better protection against condensation. These alternatives can offer improved overall performance by combining spray foam with different materials. Some advanced systems are designed for cold climates, providing a more efficient and safer solution for long-term insulation needs.
Sole Spray Foam Insulation: A Long-Term Investment
For homeowners looking for a superior approach, choosing to use solely spray foam insulation may be a better option. While it is expensive upfront, this method offers superior air sealing capabilities and higher R-values, making it a better long-term investment. Over time, spray foam insulation can provide enhanced efficiency and potentially lower energy costs, reducing the need for frequent maintenance and improving overall home insulation performance.
Cost Estimation: Making an Informed Decision
Estimating costs based on your specific needs and the rates of local contractors is crucial when selecting insulation. Understanding whether the extra expenditure for superior materials and methods is justified by the long-term benefits is essential. By comparing potential issues with flash and batt insulation, homeowners can aid their decision-making process and choose the most effective insulation for their home.
Exploring Alternative Insulation Methods
For those interested in alternatives to fiberglass batt or flash and batt, exploring options like cellulose insulation can provide valuable insights. Cellulose offers numerous advantages over traditional insulation, including superior thermal properties and better environmental performance. Homeowners looking for alternative insulation methods may find that cellulose delivers better efficiency while reducing the risk of common issues seen in flash and batt installations.
Making an Informed Choice for Your Home
Choosing the right insulation for your home depends on understanding your priorities and the specific needs of your property. While flash and batt may seem appealing due to its cost-effectiveness and hybrid benefits, homeowners should remain cautious of its limitations. Considering alternative methods, consulting knowledgeable contractors, and researching each option carefully will help ensure the best decision for long-term insulation performance.
Final Thoughts
Flash and batt insulation is a cost-effective solution that blends spray foam and fiberglass, offering energy efficiency and long-term savings. However, it also has condensation risks, gapping issues, and installation challenges, which can lead to mold or insulation failure in certain climate zones. To ensure the best outcome, homeowners should weigh alternatives, such as sole spray foam or hybrid insulation with vapor barriers. Choosing wisely, investing in quality materials, and consulting knowledgeable contractors will help create a comfortable and energy-efficient home.
FAQ
Is Flash and Batt a Good Idea?
Flash and batt can be a good idea as a value engineering approach for closed-cell spray foam wall design. However, the main issue is whether the vapor profile is properly managed to assure moisture does not turn the wall into a moisture factory. Proper installation and planning are key to avoiding potential problems.
What Are the Disadvantages of Batt Insulation?
Fiberglass batt insulation has some drawbacks, as it can be itchy and irritating to handle. Inhaling fibers may cause respiratory problems, so it is important to wear protective clothing and a mask when handling or installing it.
Do Flash and Batt Need a Vapor Barrier?
A vapor barrier helps control water content in the air, preventing it from passing through walls and condensing inside, which can lead to mold and mildew issues. Flash and batt insulation does not install enough closed-cell spray foam to fully create a vapor barrier, making it less effective in moisture control.
When Should You Not Use Spray Foam Insulation?
You should not apply spray foam insulation in unvented crawl spaces or attics without proper moisture control. If used without addressing moisture issues first, it can lead to trapped humidity, causing mold growth and structural damage over time.