Spray foam insulation is known for its ability to pay for itself over time by significantly improving energy efficiency and minimizing heat transfer within your home. Unlike traditional insulation methods like fiberglass blankets, batts, or rolls, spray foam is applied with a sprayer and expands to fill cavities, sealing air completely. This approach offers great benefits for both existing homes and newly built spaces, including a pole barn or any other structure where durability and thermal performance are key. While the price tag may seem high, it’s a premium product that provides more than just insulation—it’s an investment in long-term comfort and energy savings. Personally, I’ve seen how the added benefits can be worth paying a premium when planning for the life of your property.
How Much Does Spray Foam Insulation Cost
The average cost of spray foam insulation is around $6,080, with costs typically ranging between $3,385 and $10,960, depending on the project. The price per board foot varies based on the type of foam used. For open-cell spray foam insulation, you can expect prices between $0.45 and $0.75 per board foot, while closed-cell spray foam insulation ranges from $1.00 to $1.60 per board foot.
Many people wonder why spray foam insulation is expensive and feel frustrated with the internet’s vague claims that fail to mention the real costs. Why can’t someone talk numbers upfront? It’s true that nobody wants to call for a quote without being ready to decide, but the fact is, understanding the numbers helps people weigh the cost versus the benefits themselves. When you consider everything, from existing costs to the premium quality, spray foam might feel pricey but is often worth several times its initial cost in energy savings and comfort. As someone who has used spray foam insulation in my own home, I can confidently say that while the upfront cost can be daunting, the sealing capabilities and efficiency gains make it an excellent choice for many.
How To Estimate The Cost Of Spray Foam Insulation
When you want to estimate the cost of spray foam insulation, there are three steps you should follow to simplify the process.
- Find the square footage:
- Calculate board feet:
- Estimate the price:
Let’s discuss these steps in detail
Step 1: Find The Square Footage Of Your Project
To calculate the cost of spray foam insulation, start by determining the square footage of your project. Measure the total area to be sprayed, including spaces like basement walls, attics, exterior walls, and crawl spaces in your home. Make sure to measure the dimensions of each space carefully, as the depth of insulation directly impacts the price. Once the square footage is clear, you can move on to calculate board feet and further refine the cost estimate. Taking these steps ensures you’re prepared to accurately insulate the basement walls, crawl spaces and other areas effectively.
Step 2: Calculate Board Feet Using The Square Footage
Once you have the square footage of your project, the next step is to calculate board feet, which is how spray foam contractors base their quotes. Board feet are a dimensional measurement that includes length, width, and depth—unlike square feet, which only account for two dimensions. To calculate, multiply the square footage by the desired insulation depth, typically measured in inches, to get the total board feet needed. This is a simple but critical calculation that ensures the right amount of spray foam insulation is installed for your needs.
The board feet of your project depends on the type of spray foam you choose, such as open-cell or closed-cell. These two types are different; open-cell foam is less dense, while closed-cell foam provides more durability and insulation but comes with a higher rate per board foot. Make sure to label the number for each type, so you can apply the right rate when finalizing your estimate. Following this final step helps ensure an accurate cost assessment for your insulation project.
Certainly, let’s break down how to calculate square feet and board feet.
Square Feet (2D)
- Imagine a square.
- If each side of that square is 1 foot long, you have a square that is 1 foot wide and 1 foot long.
- To find the total area of this square, you multiply the width (1 foot) by the length (1 foot).
- 1 foot x 1 foot = 1 square foot
Board Feet (3D)
- Now imagine a board.
- This board is also 1 foot long and 1 foot wide, but it has thickness. In this case, the board is 1 inch thick.
- To find the volume of this board, you multiply the length (1 foot) by the width (1 foot) and then by the thickness (1 inch, which is 1/12 of a foot).
- 1 foot x 1 foot x (1/12) foot = 1/12 cubic foot
- Since 1 board foot is equal to 1/12 of a cubic foot, this board is 1 board foot.
Step 3: Multiply Board Feet By Cost Per Board Foot
The final step in estimating the cost of your spray foam insulation project is to multiply the total board feet by the price per board foot. For closed-cell spray foam, the rates are generally higher than those for open-cell spray foam, which typically falls within a lower price range per board foot. These prices vary depending on the insulation depths and specific application needs. Ensure your estimate accounts for the square footage and any variations in depth across different parts of the project. By following these three steps, you’ll get a rough price range that reflects your insulation needs accurately.
Factors That Can Affect Your Spray Foam Estimate?
Several factors can influence the overall estimate for spray foam insulation:
- Raw materials: The type and quality of materials significantly affect the price.
- Man-hours: The time required for installation directly impacts costs.
- Project complexity: More complex projects often mean higher expenses.
- Contractor expertise: A skilled professional contractor may charge higher rates but ensure better quality.
- Market and climate: Regional markets and weather conditions can also alter pricing.
The quote you receive from a professional contractor might be higher or lower than expected depending on these factors. For example, in areas with harsh climates, contractors may recommend additional insulation, which increases the costs. Always consider a combination of these elements and not the price alone when choosing the right contractor for your project.
Average Spray Foam Insulation Costs
National Average Cost | $6,080 |
Typical Price Range | $3,385 – $10,960 |
Extreme Low-End Cost | $2,225 |
Extreme High-End Cost | $15,600 |
The pricing of spray foam insulation varies based on the type, such as open-cell or closed-cell, and the thickness required to achieve the desired R-value. Open-cell spray foam is lighter and costs less, but closed-cell is denser, offering better energy savings—although with a higher price tag. In my experience, layering closed-cell foam in garages and attics for additional thickness helped to enhance the insulating material’s ability to prevent heat loss and regulate temperature effectively. These materials are measured in board feet, representing 1 square foot of foam 1 inch thick.
Other factors affecting prices include the size of the home, location, and the complexity of the installation. For larger houses, the costs can climb due to the increased amount of foam required to insulate. Areas like a garage or attic often involve complicated installations, increasing labor costs and the time needed to complete the project. The price per board foot typically ranges from $0.44 to $1.55, depending on the type of foam and the application. For residential construction, I’ve seen these projects fit within various budgets when planned well. Ensuring proper airflow regulation and heat flow prevention makes spray foam insulation an excellent investment for long-term energy efficiency.
Average Spray Foam Insulation Cost Per Square Foot
The average cost of spray foam insulation per square foot ranges between $1 to $5, depending on the type of foam and the project’s complexity. Open-cell foam is generally cheaper, while closed-cell foam offers more durability and better energy efficiency but comes with a higher price. For homeowners looking to improve their homes, understanding the key factors that influence costs—like the materials, size of the area, and whether it’s a whole house or just a specific space—is crucial. For example, professional installation for a big project might cost around $3,000 to $5,000, while smaller projects could be closer to $1,500 to $3,000.
Getting estimates from local contractors is essential to ensure you’re getting a good deal. Factors like the complexity of the installation and your region can impact the final cost. When planning your project, request multiple quotes to compare prices and plan your budget effectively. In my experience, working with professionals who offer clear pricing helps avoid surprises and ensures the job is done right. For homeowners, investing in spray foam insulation not only improves energy efficiency but also adds long-term value to the home.
Spray Foam Insulation Cost Estimator by Type
The cost of spray foam insulation depends on the type you choose, with open-cell being a less expensive option and closed-cell offering a higher R-value for better insulation. Open-cell spray foam typically costs between $0.45 and $0.75 per board foot, making it suitable for projects where affordability is key. In contrast, closed-cell spray foam is denser and ranges from $1.00 to $1.60 per board foot, providing superior energy efficiency with an R-value between 3.6 and 6.5. When considering your project, using an accurate estimator ensures you can plan the purchase cost effectively based on your specific insulation needs.
Type | Cost per Board Foot | Average R-value | Features |
Open-Cell Spray Foam | $0.45 to $0.75 | 3.6 | Less expensive, suitable for soundproofing |
Closed-Cell Spray Foam | $1.00 to $1.60 | 6.5 | Dense, offers better energy efficiency |
Spray Foam Insulation Cost Estimator by Thickness
Thicker applications of spray foam insulation are ideal for achieving improved energy efficiency and higher R-values. The tables below demonstrate how increasing thickness impacts the R-value range and the cost per square foot for open-cell and closed-cell spray foam.
Cost and R-value by Thickness for Open-Cell Spray Foam Insulation
Thickness (inches) | R-Value Range | Cost Per Square Foot |
1 | 3.5 – 3.8 | $0.45 – $0.75 |
2 | 7.0 – 7.6 | $0.88 – $1.30 |
3 | 10.5 – 11.4 | $1.56 – $2.90 |
4 | 14 – 15.2 | $2.08 – $3.90 |
5 | 17.5 – 19 | $2.60 – $4.90 |
6 | 21 – 22.8 | $3.07 – $5.85 |
7 | 24.5 – 29.6 | $3.64 – $6.80 |
8 | 28 – 30.4 | $4.16 – $7.80 |
9 | 31.5 – 34.2 | $4.68 – $8.90 |
10 | 35 – 38 | $5.20 – $9.75 |
Cost and R-value by Thickness for Closed-Cell Spray Foam Insulation
Thickness (inches) | R-Value Range | Cost Per Square Foot |
1 | 5 – 7 | $1.00 – $1.60 |
2 | 10 – 14 | $2.30 – $4.40 |
3 | 15 – 21 | $3.45 – $6.60 |
4 | 20 – 28 | $4.60 – $8.80 |
5 | 25 – 35 | $5.75 – $11.00 |
6 | 30 – 42 | $6.65 – $13.40 |
7 | 35 – 49 | $8.05 – $15.40 |
8 | 40 – 56 | $9.20 – $17.60 |
9 | 45 – 63 | $10.35 – $19.80 |
10 | 50 – 70 | $11.50 – $22.00 |
Also Read: How Thick Does Spray Foam Insulation Need To Be?
Spray Foam Insulation Cost Estimator by Household Area
Spray foam insulation costs vary based on the specific area of your home, such as attics, walls, or basements. Using a cost estimator helps homeowners plan their budget and choose a better option for their household. On average, the price for insulating various areas varies based on factors such as size and complexity. For example, a typical 1,500-square-foot area can cost $2,250 to $5,250, with the total cost changing based on the accessibility of the space and the insulation thickness required.
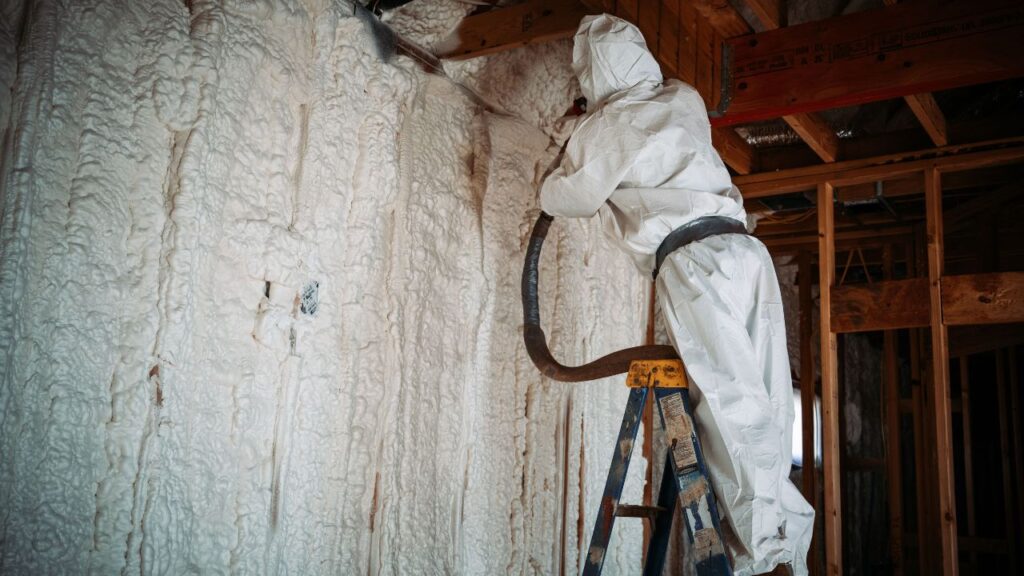
Attic
Insulating attic floor or ceiling with spray foam insulation is a great way for homeowners to enhance energy efficiency and maintain consistent temperature in their home. The cost to insulate an attic typically ranges between $1.50 and $3.50 per square foot, depending on the size and ease of access. For a 1,500-square-foot attic, costs can range from $1,700 to $5,075. Whether you’re adding a new addition, replacing damaged insulation caused by fire or rodent infestation, or simply upgrading, spray foam ensures significant energy savings and comfort. It’s an essential choice for many improvement projects.
Basement
When it comes to basement insulation, contractors and builders often recommend spray foam insulation to effectively seal off areas below ground, which are harder to insulate. Homeowners generally expect to pay between $2.50 and $5 per square foot. For a 1,000-square-foot basement, this can amount to $2,500 to $5,000. Total costs for basements typically range from $1,875 to $6,050, depending on the size and condition of the space. Applying spray foam insulation in basements helps reduce energy loss and creates a more comfortable environment in the home.
Crawl Space
For crawl spaces, which are often uninsulated, general contractors and builders frequently add spray foam insulation to improve efficiency. Homeowners pay between $1,070 and $6,170, depending on the size and access of the crawl space. Properly insulated crawl spaces, with the best insulation for crawl space, prevent air leaks and moisture buildup, ensuring better temperature control and saving on long-term energy costs. Whether you’re insulating basements or crawl spaces, investing in spray foam insulation offers significant benefits for your home.
Detached Building
Insulating detached buildings like pole barns, storage sheds, and workshops with spray foam insulation is an effective way to improve energy efficiency and temperature control in these large areas. For homeowners insulating such buildings, the costs typically range between $5,170 and $18,170, depending on the total square footage. These spaces often require significant insulation due to their size and exposure to varying weather conditions, making spray foam a practical and durable choice.
Also Read: How to Insulate a Pole Barn the Right Way
Garage
For garage insulation, builders and contractors may refrain from insulating certain spaces to reduce upfront costs, but homeowners who choose to insulate their garage walls, ceiling, and doors with spray foam insulation can expect to pay between $2,240 and $5,735. Properly insulated garages not only enhance energy efficiency but also provide better thermal protection for the rest of the home, making this an essential project for many.
Roofs
When insulating roof areas, spray foam insulation can offer excellent thermal protection for your home. However, roof insulation is often not included in general estimates for the attic, as it is considered a separate area. Homeowners who decide to apply spray foam to their roofs can expect to pay between $2,100 and $8,335, depending on the size and complexity of the project. Proper roof insulation not only enhances energy efficiency but also adds durability and protection from external weather conditions.
Shipping Containers
For shipping containers, which are becoming increasingly popular in small construction projects, spray foam insulation provides a reliable solution to maintain comfortable temperatures and prevent condensation. The cost to insulate shipping containers typically ranges between $1,300 and $2,850, making it an affordable option for these compact spaces. This application is particularly useful in extreme climates where controlling heat transfer is essential.
Walls
When it comes to wall insulation, costs can range between $2 and $4 per square foot, depending on whether old drywall needs to be removed and replaced. For a 1,000-square-foot area, homeowners can expect to spend $2,000 to $4,000. Removing drywall, applying spray foam, and reinstalling it can make the project more complex, so it’s always best to ask for quotes from trusted contractors to get a precise price. Factors like location, type of foam, and labor intensity can also cause prices to change, so getting multiple estimates ensures a fair deal.
Other Cost Factors to Consider
The cost of spray foam insulation can vary depending on the type of material and the specifics of your project. Homeowners aiming for environmentally conscious construction often look for materials that balance energy efficiency with affordability. For existing homes, factors such as accessibility of the area, electrical installations, or even pest control can increase costs. However, for a new build, these challenges are typically minimized, making the installation process smoother and potentially more cost-effective. Properly understanding these cost factors can help in planning your project effectively.
Spray Foam Material
When choosing the right spray foam material, there’s a variety of insulating materials available that cater to different needs. Consumers can choose materials that prioritize environmental impact, energy efficiency, or specific cost goals. Certain materials are better suited for projects in unique locations of the home, such as basements or attics. Selecting the right material ensures your insulation project aligns with your goals and delivers the desired results while staying within your budget.
Polyurethane Foam Insulation
Polyurethane spray foam insulation is one of the most common types on the market. Costing between $0.44 and $1.50 per board foot, it is a cost-effective option for homeowners who prioritize affordability while addressing their environmental impact. This type of insulation is widely available and offers reliable energy efficiency, making it a popular choice for various projects.
Soybean and Vegetable Oil-Based Spray Foam Insulation
For homeowners seeking environmentally friendly options, soybean-based spray foam insulation is a great choice, costing $1.15 to $2.50 per board foot. Although it comes with a slight increase in costs, it effectively balances eco-conscious goals with insulation needs.
Similarly, vegetable oil-based spray foam insulation, while similar to soybean options, costs between $1.50 and $3.00 per board foot. This product is less readily available but offers a friendly environmental footprint, making it ideal for specific projects.
Water-Based Spray Foam Insulation
A newer option in the insulation world, water-based spray foam insulation is considered the best for the environment. It costs between $0.50 and $2.50 per board foot and offers good durability and efficiency, though some of its properties are slightly negated compared to oil-based products. Homeowners looking for a premium material may find this a suitable option despite the slight cost increase.
Mold Removal
When installing spray foam insulation, addressing mold removal can significantly affect the overall cost. A contractor may need to remove mold before starting the process, with costs ranging from a few hundred dollars to several thousand, depending on the area size and severity of the issue. On average, homeowners can expect to spend between $1,100 and $3,400 for professional mold removal. For smaller spaces, such as a 10×10 feet area, a kit from a local home improvement supplier can be a cost-effective solution to tackle the problem independently.
New Construction vs. Existing Installs
In new construction, installers have easier access to all areas of the home, making the process of installing insulation more straightforward. However, for existing homes, homeowners may need to consider the removal of old insulation, which can increase costs. Accessibility to different areas, such as walls and ceilings, can be a challenge, especially when working around electrical conduit or addressing pest control issues. These factors can make insulation projects in existing homes more complex compared to new construction.
Removal of Old Insulation
In new construction, the process of installing spray foam insulation is often smoother since installers have better access to all areas of the home. This makes it easier to apply insulation in walls, ceilings, and other spaces without extra preparation. For existing homes, however, additional steps like the removal of old insulation may be required. This can be due to moisture issues, fire damage, or even a pest problem. Homeowners should plan their budget accordingly, as removal and disposal can add $1 to $2.15 per square foot to the overall costs. If asbestos is present, specialized asbestos removal may further increase expenses.
Accessibility and Electrical Considerations
In many existing homes, limited accessibility to areas like tight crawl spaces or high-pitched roofs can make the installation process more challenging. Homeowners may need to remove drywall or siding to create easier access for the application of spray foam. This can result in additional costs, especially during remodeling projects. Another critical consideration is electrical wiring. Homeowners must take care to avoid disturbing electrical cabling during the application process, as improperly handled wiring could hinder future installations or damage the system. Proper planning and consultation with professionals can help address these challenges effectively.
Spray Foam vs. Other Insulation Options
Spray foam insulation is a top choice for its ability to seal gaps, provide higher R-values, and improve energy efficiency. While it is a great fit for projects requiring complete air sealing, it can be more expensive compared to other types of insulation like fiberglass, cellulose, or rigid boards. Fiberglass is a budget-friendly option that offers good energy efficiency, while cellulose, made from recycled paper, is more eco-friendly with reasonable costs. Rigid foam boards provide excellent performance in sealing odd shapes but may require additional effort during installation. Choosing the right insulation material depends on your project needs, budget, and long-term energy-saving goals.
Insulation Type | Material Cost | Installation Cost | Energy Efficiency | Best Uses |
Spray Foam | High | High | Excellent | Sealing gaps, achieving high R-value, air sealing |
Fiberglass | Low | Moderate | Good | General home use, budget-friendly |
Cellulose | Moderate | Moderate | Very Good | Eco-friendly projects, recycled materials |
Rigid Foam Boards |
High | Moderate | Excellent | Odd shapes, areas needing durability |
Professional vs. DIY Spray Foam Insulation Installation?
DIY Spray Foam Insulation: Costs and Considerations
DIY spray foam insulation can be a way to save money, but it comes with its own challenges. The cost for DIY insulation is typically $1 to $2 per square foot, depending on the kit size and type of foam. For a small project, you can expect to spend between $300 and $600, while insulating a whole house might cost $1,500 to $2,000. DIY kits usually include:
- Chemicals
- Dispensing gun
- Nozzles
- Protective gear
However, there are extra costs to consider, like safety gear, prep materials, and cleaning supplies, which may include a respirator, goggles, gloves, and protective clothing.
Installing spray foam insulation yourself requires skill and care to avoid common mistakes like leaving air gaps or creating moisture problems. These issues can make the insulation less effective and may lead to further repairs. Hiring experts who have the right tools, knowledge, and understanding of building codes can sometimes be a better option, especially for big or complex projects. While DIY can help cut labor costs, it comes with the risk of mistakes that may cost more time and money in the long run. For homeowners who want insulation that works effectively, hiring professionals ensures the job is done right and delivers energy savings over the long run.
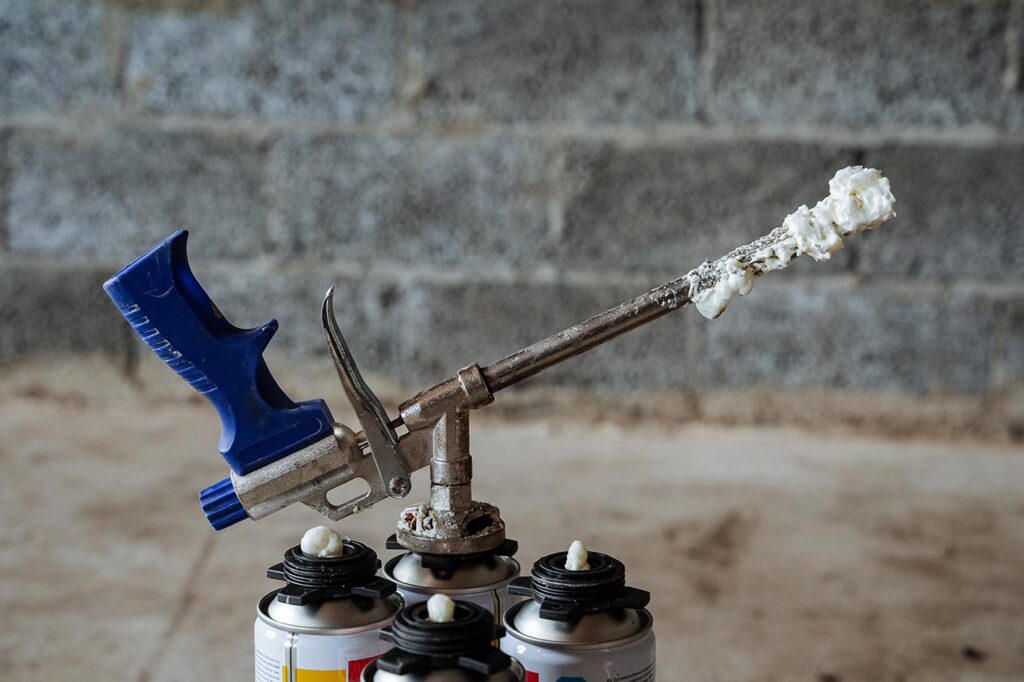
Professional Spray Foam Insulation Installation
Choosing professional spray foam installation can help save time and ensure quality results. By hiring insulation contractors, you gain access to their expertise and tools, which can make your project more efficient and effective. Professionals handle complex tasks with precision, ensuring the insulation is applied correctly to deliver optimal energy savings and durability. This approach is especially valuable for larger or more intricate installations where mistakes could be costly.
Finding a Reputable Contractor
When finding a reputable contractor, start by researching local insulation contractors and looking for reviews, certifications, and references. Compare prices from at least three contractors before deciding to ensure you’re getting the best value for your money.
The Installation Process
The installation process includes several steps, starting with site prep to protect the area. Professionals then mix and heat the foam components, carefully applying spray foam to the necessary spots. Afterward, the foam is left for curing and trimming, followed by a thorough clean-up and a final check to ensure everything is completed to a high standard.
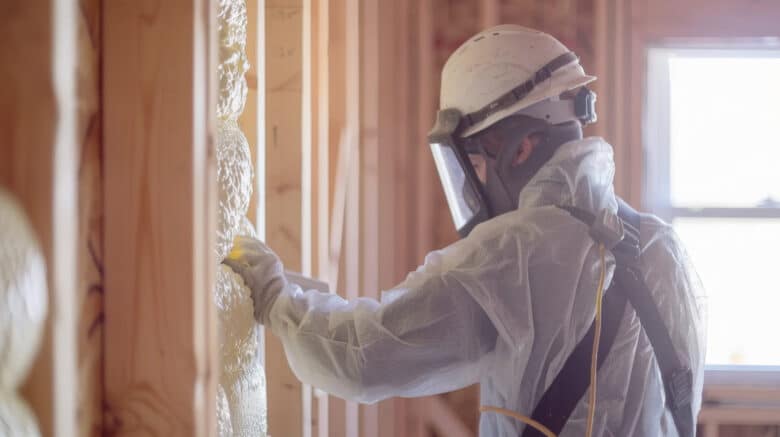
Cost of Spray Foam Insulation by Location
Spray foam insulation costs can vary significantly across the United States due to regional factors like climate, building codes, and local market competition. In colder areas, people often spend more to fight harsh winters and achieve lower energy bills. For example, regions with stricter building codes requiring higher R-values will typically see higher costs. Additionally, cities with more contractors tend to offer better prices due to increased competition, while rural areas with fewer choices might have higher prices.
Here’s a breakdown of average spray foam insulation costs per square foot across major regions:
Region | Open-Cell Cost (per sq. ft.) | Closed-Cell Cost (per sq. ft.) |
Northeast | $1.50 – $2.50 | $3.00 – $4.50 |
Southeast | $1.25 – $2.25 | $2.75 – $4.25 |
Midwest | $1.35 – $2.35 | $2.85 – $4.35 |
West Coast | $1.75 – $2.75 | $3.25 – $4.75 |
Commercial projects and large orders in cities often have lower costs per square foot, especially for big projects, due to economies of scale. Planning and considering regional factors can help homeowners estimate the cost and optimize their budget effectively.
Tips for Reducing Spray Foam Insulation Costs
Timing Your Installation
Start by timing your installation during off-peak seasons, like fall or spring, when contractors are less busy. This is when many companies offer discounts, which can lead to better prices and help you save money. Planning your project strategically during these times ensures you get the best value for your budget.
Combining with Other Home Improvement Projects
Another effective strategy is combining spray foam insulation with other home remodeling services. When you bundle these services, contractors often provide package deals, reducing the total cost. This approach not only lowers labor costs but also optimizes your spending for multiple home improvements at once.
Taking Advantage of Rebates and Incentives
Look into local and federal energy-efficiency programs, as many offer rebates or tax credits for installing spray foam insulation. These incentives can significantly reduce the upfront cost, making it easier to stay within your budget while improving your home’s energy efficiency. By utilizing these strategies, you can turn an expensive project into a more manageable and cost-effective investment.
Cost-Saving Strategy
Adopting the right cost-saving strategy can help you manage your spray foam insulation expenses while maximizing its benefits.
Cost-Saving Strategy | Potential Savings | Key Benefits |
Off-Season Installation | 10% – 15% | Lower costs during less busy periods |
Bundling Projects | 5% | Reduced labor costs, combined services |
Rebates & Incentives | Up to 30% | Significant cost reductions upfront |
By combining these strategies, homeowners can save on spray foam insulation costs while achieving a more energy-efficient home.
Final Considerations for Spray Foam Insulation
When planning for spray foam insulation, it’s important to remember that every quote depends on your unique project. The cost varies by type, such as open-cell foam or closed-cell foam, with the former being cheaper but less insulated. Factors like location, size, and the climate of your area also affect pricing.
To get an accurate estimate, consult a spray foam contractor familiar with your market. They can help you understand how factors like depth, size, and additional work could impact the final cost, and advise on available rebates or financing options to manage the upfront investment.
Looking to connect with a reliable spray foam insulation contractor? Contact us today, and we’ll refer you to trusted professionals who can provide a detailed quote tailored to your project needs. Start saving on energy bills while improving your home’s comfort and air quality!
FAQ
How much does it cost to spray foam for 1000 square feet?
Area Size (Square Feet) | Average Cost (Installed) |
1,000 | $1,000 – $5,000 |
1,500 | $1,500 – $7,500 |
2,000 | $2,000 – $10,000 |
2,500 | $2,500 – $12,500 |
Is spray foam insulation worth the extra money?
Spray foam insulation might have a higher cost compared to traditional options, but over time, it pays back in significant energy savings. Beyond the financial benefits, it also enhances the comfort of your family, making it a valuable investment.
How much does it cost to spray foam 600 square feet?
Square Footage | Cost |
600 | $600–$2,700 |
1,200 | $1,200–$5,400 |
2,000 | $2,000–$10,000 |
How much does spray foam insulation cost?
The average cost of spray foam insulation per square foot ranges between $1.50 and $4.50, with some options priced as high as $5.00 per square foot meaning that insulating a 1,000 square foot attic would range from $1,500 to $4,500 depending on the project size and requirements.