Spray foam insulation often raises eyebrows due to its higher price tag compared to traditional insulation methods. This method of insulating a home makes it notably expensive, but it’s essential to explore why this is the case. Unlike other options, spray foam offers superior insulation properties and energy efficiency advantages that justify the extra cost. Its ability to create an airtight seal enhances the effectiveness of insulation, making it a worthwhile investment for those looking to implement cost-saving measures without compromising on quality.

Why is spray foam so expensive? Factors such as the complex application process and the use of high-quality materials contribute to its higher cost. Spray foam isn’t just a product—it’s a complete solution that requires precise installation techniques, directly affecting the budget. By understanding these factors, homeowners can see how the upfront expense leads to long-term savings on energy bills, validating its overall value in the market.
Understanding the Cost of Spray Foam Insulation
Breaking Down Spray Foam Insulation Pricing
Spray foam insulation is recognized as more expensive compared to other insulation types, but its pricing structure is specific and varies based on several factors. The cost of spray foam insulation can range widely depending on whether you choose open cell or closed cell foam. For open cell foam, prices might be between $0.25 and $0.75 per board foot, while closed cell foam can cost between $1.15 and $1.75 per board foot. It’s important to note these are costs per board foot, not per square foot, which means the price can add up quickly depending on the project’s size and foam depth required.
For different applications, the cost adjustments are significant. For instance, insulating an exterior wall may cost between $2.25 and $3.38 per square foot using open cell foam, whereas an attic application could run between $5.00 and $7.50 per square foot. This variation is largely due to the quantity of foam used and the specific depths needed for effective insulation. Spray foam’s cost also varies by the type of project and the type of foam used, which is why calculating the total board feet is crucial to estimate the project budget accurately.
Why Spray Foam Is a Premium Insulation Option
Superior Performance and Efficiency
Spray foam insulation is often described as a premium product due to several compelling factors that distinguish it from traditional insulations like fiberglass batts and blown-in products. The first standout feature is its superior insulating performance. Spray foam delivers not only high R-value, a metric used to measure the ability to resist conductive heat transfer, but also an airtight seal. This seal is critical in preventing heat exchange through convection and radiation, areas where traditional materials often fall short.
Cost Factors and Application Techniques
Another reason spray foam is considered a premium choice involves the manufacturing costs and the equipment required to apply it properly. Unlike simpler insulations that can be manually placed or unrolled, spray foam must be applied using specialized equipment that insulates and air-seals a space simultaneously. This dual capability not only enhances the effectiveness of the insulation but also contributes to its higher cost.
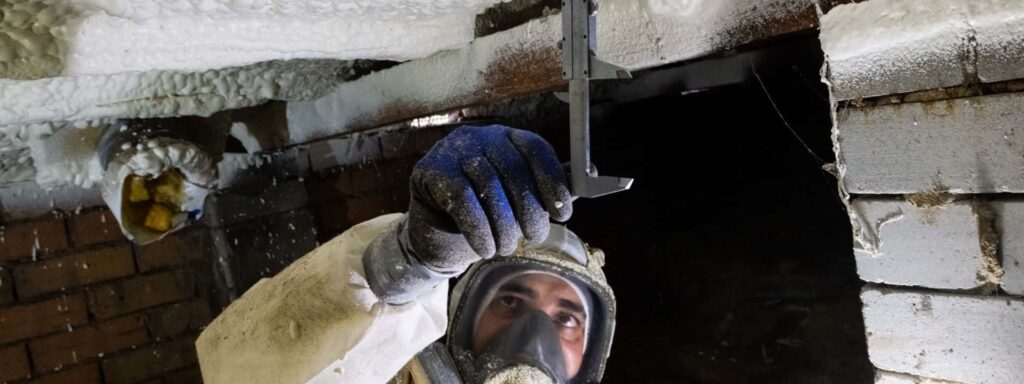
Additionally, spray foam insulation is more than just a barrier against cold and heat; it enhances structure integrity, contributes to lower energy bills, and improves air quality by creating a more consistent indoor climate free from drafts. These benefits underscore why spray foam is priced higher than alternatives that lack the same comprehensive air-sealing capabilities. Unlike options that might seal with can foam or caulking, spray foam’s application ensures every nook and cranny is covered, making it an all-in-one solution for insulation and air sealing.
Complex Manufacturing Process
Spray foam insulation stands out among insulation products primarily due to its manufacturing costs. Unlike materials like recycled cellulose or glass fibers, which are relatively straightforward to produce, spray foam requires raw chemical materials that are inherently more expensive. The production process isn’t just about mixing ingredients; it involves chemical processing facilities that are costly to build and maintain. These facilities must adhere to stricter safety and testing protocols, significantly increasing the overhead. In contrast, plants creating fiberglass or cellulose insulation do not face such high safety and testing costs, as those industries don’t deal with complex chemicals.
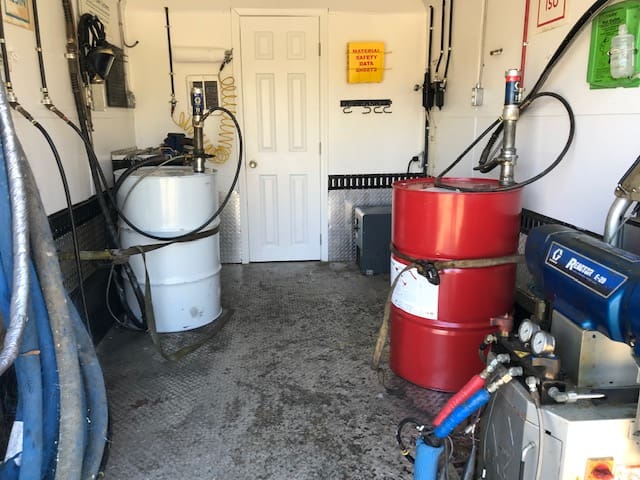
Specialized Installation Equipment
Another aspect that adds to the expense is the installation process. Spray foam isn’t just another insulation product that can be cut and fitted into place. It is both a product and a service that requires specialized equipment for safe and effective installation. This equipment, housed in a spray foam rig—a sophisticated setup that can be a truck or trailer—travels to job locations. It contains all necessary materials and equipment to safely apply the foam. Such rigs are equipped with devices that monitor temperature, pressure, and ratio, ensuring the foam’s quality. The cost for one of these rigs can range from $60,000 to $100,000, a significant investment for any contractor.
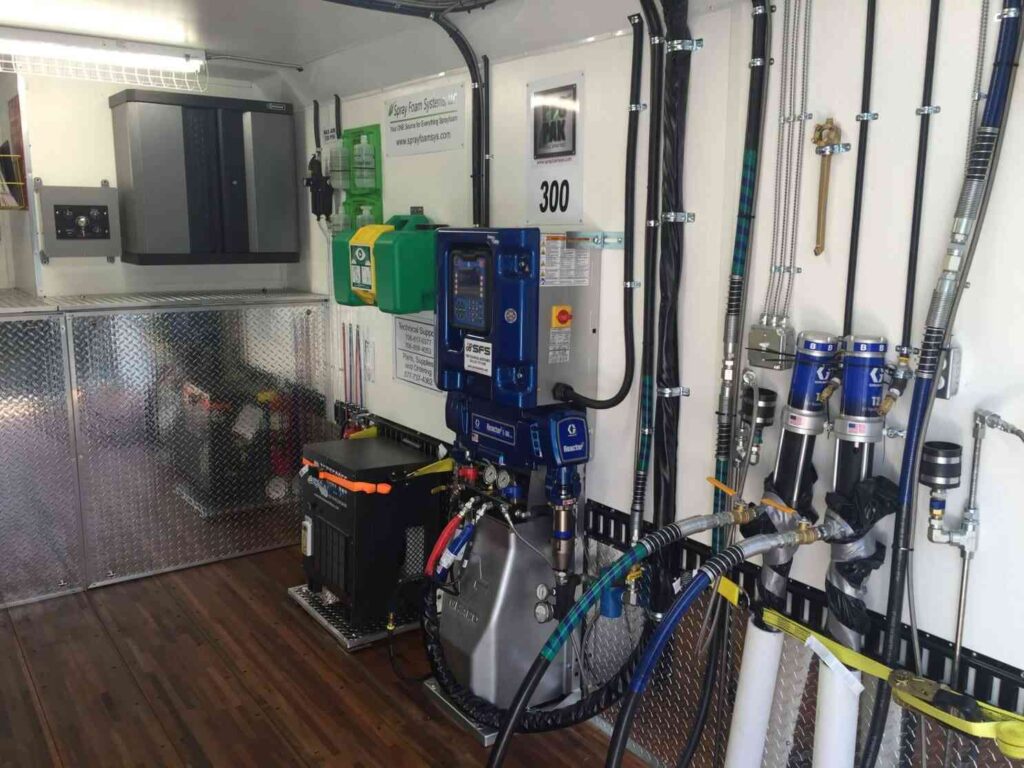
Each of these factors—the advanced manufacturing process and the need for specialized application equipment—contributes to why spray foam insulation is more expensive compared to traditional options, emphasizing its status as a premium product.
Factors Affecting Spray Foam Pricing
To understand why spray foam insulation is more expensive than other insulation products, it’s essential to consider the numerous factors impacting its pricing. The manufacturing costs, quality of materials, and specialized application methods are vital elements that influence how it’s priced. Contractors must also account for the complexity and size of the project, which can determine the overall cost. As homeowners dive into bids, they realize that these factors play a significant role in the bottom line, making spray foam a worthwhile yet expensive choice due to its superior performance and durability.
Material Quality and Quantity
Spray foam insulation is known for its high-quality materials and superior insulation properties, which naturally lead to a higher cost. The quality and quantity of raw materials used in manufacturing spray foam play a significant role in its pricing. These materials are specialized and costly, and the complex chemical processes required to create effective spray foam add to the overall expense of the installation. It’s common sense that better materials cost more, and this directly contributes to why spray foam insulation is priced higher than less effective options.
Cost Calculation and Misconceptions
Many people believe that the cost of spray foam relates to the volume used, much like opening a 2-liter bottle of soda—once it’s opened, you are charged for the full amount. However, this is a common misconception. In reality, spray foam contractors calculate the cost based on the liquid chemical needed to create the required amount of foam for the project. The pricing is determined per board foot, considering the depth and square footage of the space being sprayed. This method ensures that homeowners are not overcharged, aligning the charge with the actual amount of insulation installed, rather than just the potential maximum capacity of a 55-gallon drum.
Labor and Complexity Considerations
When evaluating spray foam quotes, it’s crucial to understand how contractors break down labor costs. Often, these costs are based on man-hours and the complexity of the project. Larger or more complex projects that require intricate application techniques may see higher pricing due to the additional time and labor involved. Some contractors may charge separately for prep work or existing insulation removal, significantly impacting the overall cost.
Influence of Location and Safety Requirements
The project’s geographical location also significantly influences spray foam pricing. Factors such as local building codes, the availability of skilled labor, and transportation costs can vary by area, each adding to the cost. Additionally, projects with specific safety requirements or those needing additional specialized equipment due to building codes can increase costs, particularly for complex or commercial jobs.
Energy Efficiency and Expertise
Lastly, the project’s desired energy efficiency goals can influence pricing. Achieving higher R-values might necessitate additional insulation material and well-trained, qualified contractors, pushing up costs. Not every contractor is equally knowledgeable or qualified; those who are can charge higher due to their expertise, which ensures the job is done right. This is reflected in higher bids that, while initially more costly, may represent a better value over time due to the quality and durability of the installation.
These varied factors underscore why spray foam insulation can be an expensive option, yet one that offers substantial long-term benefits for those looking to enhance their property’s insulation effectively.
Application Method and Material Usage
The application method and the type of foam used play significant roles in spray foam insulation pricing. Choosing between open-cell and closed-cell spray foam affects both the technique of installation and the project’s overall cost. Open-cell foam, less dense and able to cover more area from a single 55-gallon drum, typically costs less per unit but may not provide the same level of insulation as closed-cell foam, which has a higher density and provides better thermal resistance. The type of foam chosen often hinges on specific project details such as whether the application is above-grade in attics and roofs, or below-grade in basements and crawl spaces.
Impact of Travel Time and Project Urgency
Travel time is another critical factor that can vary significantly based on location and market conditions. If the closest contractor is over four hours away, travel time can become a notable part of the quote, especially in areas where several contractors aren’t available within a reasonable driving distance. Moreover, the project’s timeline can also influence the cost. Quicker turnaround times and expedited installations demand more resources and labor, making them more expensive.
These variables—application methods, material choice, travel time, and project urgency—all contribute to why spray foam insulation can appear costlier compared to other insulation types. Each factor needs careful consideration to understand how it impacts the final quote and to ensure that the chosen insulation solution works best for the specific needs of the structure.
Benefits Of Spray Foam Insulation
Superior Energy Efficiency and Comfort
Spray foam insulation is highly regarded for its outstanding energy efficiency, a standout feature that justifies its higher initial cost. This type of insulation excels in reducing heating and cooling costs by creating an airtight barrier that prevents drafts and minimizes energy waste. With its high R-value and superior air-sealing properties, spray foam provides better thermal resistance than traditional insulation methods, allowing homeowners to maintain a comfortable indoor temperature all year round without relying on excessive heating or cooling. This makes it a superior choice for those looking to enhance their home’s energy efficiency.
Durability and Cost Effectiveness Over Time
Another significant benefit of spray foam insulation is its long-term durability. Unlike other insulations that might sag or deteriorate over time, spray foam can last decades without showing significant deterioration, contributing to its overall value. The long-term energy savings provided by this insulation can significantly offset its upfront cost, leading to lower energy bills and substantial cost savings over time. This durability not only ensures a continuous energy savings but also a comfortable living environment, making spray foam a cost-effective solution in the long run.
These features highlight why spray foam insulation, despite its upfront investment, is celebrated for its efficiency and cost-saving potential, marking it as a wise investment for those prioritizing a sustainable and comfortable home environment.
Affordable Spray Foam Alternatives
Budget-Friendly Insulation Choices
For those looking to insulate their homes without having to break the bank, several affordable alternatives to spray foam are available that offer cost-effective solutions.
Fiberglass Insulation: An Economical and Effective Option
Fiberglass insulation is a popular and budget-friendly alternative that consists of tiny glass fibers and is available in rolls or batts. It’s easy to install and can effectively insulate your home, providing both thermal and sound insulation. This makes it an excellent choice for homeowners and contractors seeking suitable insulation material that meets budgetary needs without compromising on effectiveness.
Cellulose Insulation: A Sustainable Option
Another cost-effective option is cellulose insulation, made from recycled paper products, such as newspapers, and treated with fire-resistant materials. This type of insulation is typically blown into walls, attics, and crawl spaces, filling gaps and providing excellent insulation. Cellulose insulation is especially known for its thermal and sound insulation properties, making it a practical and environmentally friendly alternative for those looking to enhance their home’s energy efficiency and comfort.
Mineral Wool Insulation: A Cost-Effective Substitute
Mineral wool insulation, including rock wool and slag wool, offers a budget-friendly price while delivering excellent fire resistance and thermal insulation. Made from spun fibers of rocks and minerals, this type of insulation comes in batts or loose-fill formats and is celebrated for its durability and ease of installation. Mineral wool is not only easy to install but also provides good sound insulation, making it an ideal affordable alternative for those considering different insulation options. It balances cost and effectiveness efficiently, making it a compelling choice alongside other materials like fiberglass and cellulose.
Spray Foam Kits: DIY Cost Savings
For those who prefer the benefits of spray foam insulation but are looking for a more affordable option, spray foam kits present a viable solution. These kits allow homeowners to apply the insulation themselves, reducing labor costs significantly. Following the essential instructions for proper installation is crucial to ensure effectiveness without compromising on quality. Spray foam kits are especially advantageous for making decisions based on budget and specific insulation needs, offering a cost-effective way to achieve similar benefits as professional spray foam application while exploring alternatives that fit one’s financial and practical requirements.
These alternatives provide practical options for those looking to insulate their spaces without the high cost associated with professional spray foam installation, ensuring that both safety and efficiency are maintained.
Final Thoughts
Spray foam insulation carries a high cost due to several factors that impact its pricing. This type of insulation is a premium product with higher manufacturing costs compared to more traditional insulation methods like fiberglass or cellulose. The complexity of the installation process also adds to the expense, whether the project is a straightforward installation or a more complex job. Contractors need to use specialized equipment and techniques to deliver a high-quality finished product, which can influence the final price significantly.
While spray foam may not be the most affordable option initially, it is important for homeowners and contractors to consider its long-term benefits. Spray foam offers exceptional energy-saving potential and durability, which can offset the lower upfront costs of other insulation types over time. Those making final decisions on insulation should weigh these benefits alongside budget-friendly solutions to determine the best approach for their specific needs and financial constraints. This holistic view helps explain why spray foam remains a favored choice despite its initial cost
FAQ
Is Spray Foam Insulation Worth the Money?
Yes, spray foam insulation is worth it despite the cost, as it pays back over time through energy savings. It also adds comfort for your family, making the price worthwhile compared to traditional options.
What Are the Negatives of Spray Foam?
While spray foam insulation is a good insulator for keeping warm and cool, it has downsides like potential health issues, ventilation problems, environmental damage, and a lower home valuation. It may also make securing a mortgage more difficult, outweighing some of its benefits.
Why Is It Hard to Sell a House With Spray Foam Insulation?
Many contractors and homeowners believe houses need to breathe, raising concern that spray foam insulation makes them too airtight. This causes some buyers to avoid the house entirely or skip bidding.
Is It Cheaper to Spray Foam Insulation Yourself?
Doing spray foam insulation yourself can be cheaper since you save on labor costs. However, hiring a professional ensures expertise and skilled labor, which might reduce mistakes and the total cost of the project in the long run.